بخارات حاصل از ضایعات پخته شده در دیگ پخت که درحین پخت خارج میگردد از دستگاه کندانسور عبورداده میشود و بدین ترتیب بخار حاصله تقطیر شده و بصورت آب از شبکه خارج میگردد.
کندانسور
سیلندر اصلی از لوله به قطر ۶۰ سانتیمتر ساخته میشود و تعدادلولههای شبکه داخلی ۱۲۰ عدد میباشد.
تجهیزات بوگیر تبدیل ضایعات کشتارگاههای دام و طیور
ماشینآلات تولیدی ما شامل خطوط تولید پودر گوشت حاصل از ضایعات کشتارگاهی دام و طیور و همچنین ساخت کلیه تجهیزات مربوط به تولید پودر ماهی و انواع بالابر و آسیاب چکشی و پرهای و سایکلونهای غبارگیر و فنهای سنتریفوژ با قدرتهای بالا و پرسهای تحتفشار جهت آبگیری از تفالهها بصورت اسکرو و کلیه تجهیزات تولید پودر خون و استخوان و انواع دیکانترها و سیستمهای انتقال مواد میباشد.
با توجه به سابقه این شرکت در امر تولید ماشینآلات تولید پودر گوشت و ماهی و مواد پروتئینی دیگر نظیر پودر خون و استخوان و چربی صنعتی و طیف وسیعی از دیگر ماشینآلات مواد غذائی در رابطه با خوراک انسانی و تغذیه دام و طیور و yekrang co
مشاهده تاثیرات نامطبوع اینگونه پروسههای تولید بر محیط زیست. در صدد رفع مشکل با بهرهگیری از سیستمی ایدهآل که هم در بر گیرنده هزینه اندک و هم برطرفکننده همه مشکلات مبتلا به تولید کنندگان باشد بر آمدیم.
با گرد آمدن متخصصان مرتبط و با بررسی همه راههای دفع بوهای زائد سیستم کاملی را طراحی و تولید و در یکی از کشتارگاههای صنعتی بزرگ استان گیلان نصب کرده و در بحرانیترین شرایط کاری تست نموده و تمام بوهای نامطبوع حاصل از تولید را حذف نمودیم.
شایسته میباشد از بذل مساعدتهای بیشمار شرکت تعاونی مرغداران استان گیلان علیالخصوص هیات مدیره و مدیر عامل محترم شرکت تشکر نموده و موفقیت ایشان را در کلیه امور از جمله کمک به پژوهشگران و مبتکران خواستار باشیم.
بوگیروبوسوز
بیتردید وجود بوی نا مطلوب را میتوان جزء آلایندههایی طبقهبندی کرد که تاثیر منفی آن بر کیفیت زندگی مشهود است. از آنجا که فرایند تولید پودر گوشت و ماهی بوی بسیار نا مطلوبی ایجاد میکند کنترل بو از اولویتهای مهم زیستمحیطی این کارخانهها میباشد.
روشهای رایج حذف بو در این واحدها بر مبنای ترقیق یا حذف ناقص آلایندهها به شکل پنهانسازی شستشو با آب و سوزاندن میباشد که راندمان کنترل در این موارد پائین بوده و نمیتواند مشکل را حل کند. خروجی شامل بخار آب ترکیبات آروماتیک سولفید ئیدروژن و تریمتیل آمین و… میباشد.
این بخارات از لحاظ وزنی ۷۰ درصد وزن ماده خام اولیه را به خود اختصاص میدهد. هدف از مطالعات انجام پذیرفته
ارایه روشی برای حذف کامل بو از خروجی این کارخانهها میباشد. روش ارائهشده مبتنی بر جداسازی ذرات جامد خروجی از پخت توسط سایکلون میعان بخار خروجی از سیستم با استفاده از مخازن جداکننده و کندانسورها همچنین جذب هرگونه رطوبت و بو در بخش پایانی فرایند بوگیری توسط مواد جاذب، یعنی ستون سیلیکا ژل و کربن اکتیو میباشد.
راندمان سیستم ۱۰۰ درصد میباشد که سهم درصدی راندمان حذف در هر یک از بخشهای فرایند با در نظر گرفتن نوسانات دمای محیط و فشار خروجی دیگ پخت در مخازن جداکننده گاز و مایع و سایکلونها ۱۵ درصد و در مبدل حرارتی ۶۵ درصد و در کویل مبرد ۱۰ درصد و در ستون کربناکتیو و سیلیکا ژل کمتر از ۱۰ درصد به دست آمده است.
کلمات کلیدی: آلودگی هوا، کنترل بو، پودر ماهی، پودر گوشت، میعان
حضور یک یا چند عامل نامطلوب در هوا با غلظت و طول زمانی که ممکن است برای سلامتی انسان و دیگر موجودات زنده مواد و مصالح اثرات زیانآور داشته باشد یا موجب کاهش لذت از زندگی و رکود در فعالیتهای اقتصادی و صنعتی شود میتواند به عنوان تعریف آلودگی هوا مطرح شود.
منشا اصلی آلایندهها فعالیت انسانی میباشد. این فعالیتها رابطه نزدیکی با الگوی مناسب زندگی دارد و محدود کردن آنها به ندرت در دستور کار برنامهریزان قرار میگیرد. رویکرد اکثر کشورهای صنعتی ادامه فعالیتها و کنترل آلایندهها میباشد. از آنجایی که در فرایند تولید پودر ماهی و پودر گوشت بوی بسیار نامطلوبی ایجاد میشود و کارخانههای تولید آن بنا به ملاحضات اقتصادی موقعیت جغرافیایی و وضعیت پراکندگی جمعیت در مناطق شمالی کشور اجباراً در کنار نقاط مسکونی و یا گردشگری احداث میشود کنترل بوی نامطلوب آنها از اولویتهای مهم زیستمحیطی این کارخانهها میباشد.
پودر ماهی و پودر گوشت به عنوان مکمل پروتئین در جیره غذائی دام و طیور مورد استفاده قرار میگیرد. پودر ماهی از انواع مختلف ماهی نظیر شاهماهی ساردین کیلکا و پودر گوشت از ضایعات تولید گوشت در کشتارگاههای مرغ و دام تولید میشود.
محصولات تولیدی شامل موارد زیر میباشد:
- الف) پودر ماهی
- ب) پودر گوشت حاصل از ضایعات کشتارگاههای طیور
- ج) پودر گوشت حاصل از ضایعات کشتارگاههای دام
- د) پودر خون
الف) پودر ماهی
نحوه تولید
۱. پیوسته:
پخت: در این بخش حرارت عمده پروتئین موجود را لخته و با گسستن دییواره سلولی سبب میگردد در مقایسه با محصول خام مقدار بیشتری آب و روغن خارج شود. تنظیم دما و زمان حرارت دادن و سرعت تولید تاثیر مستقیم در کیفیت محصولات تولیدی دارد.
پرس: در این مرحله با استفاده از یک ماردون اسکرو و با استفاده از نیروی الکترو موتور حداکثر آب و مایع از فاز جامد جدا میگردد. مایع پرس حاوی ۷۰ درصد ماده خام که شامل ۷۸ درصد آب و ۱۶ درصد روغن و ۶ درصد ذرات کوچک معلق میباشد و کیک پرس شامل ۵۰ تا ۵۵ درصد آب و ۳ تا ۴ درصد روغن میباشد.
جداسازی مایع پرس: جداسازی این مایع به سه قسمت تشکیلدهنده آن یعنی آب و روغن و ماده خشک لجنی به وسیله سانتریفوژ یا سپراتور انجام میگردد. جداسازی روغن در این مرحله سبب تولید آب چسبناک Stick Water میگردد. که ۵۰ درصد ماده خام را دارا میباشد و ۲۰ درصد پودر نهائی از آن استحصال میگردد.
تبخیر – تغلیظ: توسط سیستم جدا گانهای در چند مرحله که منوط به کیفیت آبگیری در پرس میباشد مایعی با ویسکوزیته بالا حاصل میگردد که یا مستقیماً وارد بازار میگردد یا در خشککن به کیک پرس اضافه میگردد. بخشی از بوی نامطبوع حاصل از تولید آب چسبناک میباشد.
خشک کردن: دو روش مستقیم و غیر مستقیم در خشک کردن مورد استفاده قرار میگیرد. که روش غیر مستقیم بعلت کنترل دشوار پروسه تولید عملا متروک گردیده است. در روش غیر مستقیم با نیروی بخار با کاهش رطوبت تا حدی که آب باقیمانده قادر به تامین نیازهای میکر ارگانیسمها نباشد عمل خشک کردن انجام میپذیرد. و افزایش پایداری و ماندگاری با افزودن آنتیاکسیدان میسر میباشد.
آسیاب کردن: برای تهیه محصول یکنواخت و مناسب جهت هموژن کردن و هوادهی مطلوب هنگام خروج از خشککن توسط اسکرو بالابر از یک دستگاه آسیاب استفاده میگردد.
۲. تولید پودر با استفاده از دستگاه بچ:
برای یککاسه کردن سیستم و تجمیع ماشینآلات و به طبع آن کاستن از هزینهها و بالابردن بهرهوری از یک سیستم بنام بچ استفاده میگردد.
در این روش سیستمهای پخت و پرس حذف گردیده و کلیه فرایند تولید در یک دیگ پخت انجام میگیرد. در این سیستم که هماکنون در صنایع بالاترین درصد کار بری را بخود اختصاص داده است راندمان تولید بالاتر از سیستم ذکر شده بالا میباشد. و همچنین هزینه نگهداری و تعمیرات بسیار پائینتر میباشد.
ب) پودر گوشت طیور
تولید پودر گوشت توسط همان ماشین بچ انجام میپذیرد با این تفاوت که در زمان تعیین شدهای مخلوط در حال پخت تحت فشار قرار گرفته تا آخرین نسوج و بافتها از یکدیگر جدا گردد. مقدار این زمان بستگی به نوع مواد اولیه دارد.
ج) پودر گوشت دام
کلیه پروسه پخت مطابق با شرایط تولید پودر گوشت طیور میباشد.
د) پودر خون
این محصول نیز در فشار اتمسفر توسط دستگاه بچ تولید میگردد.
تمام سیستمهای ذکرشده دارای بخار خروجی حاصل از تولید بوده و میزان این خروجیها در مقایسه با یکدیگر در تولید پودر گوشت با نوسانات شدیدتری بعلت تحت فشار قرار گرفتن همراه میباشد.
کلیه بخارات و مایعات خروجی از سیستمهای ذکرشده دارای بوی نامطبوع و با آلایندگی محیط زیست میباشد.
کندانسور و بوگیر و بوسوز
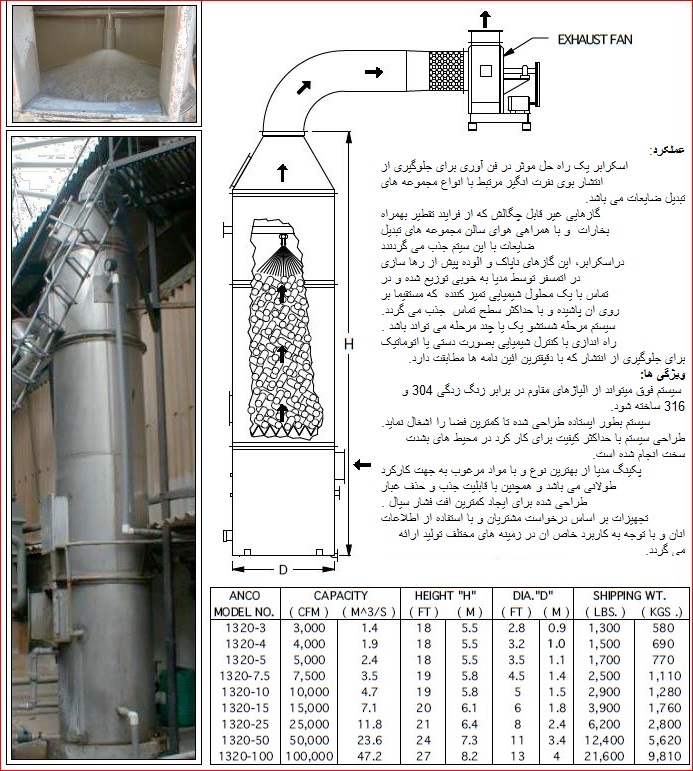
کنترل بوی حاصل از تولید محصولات
امروزه سه روش کلی برای کنترل بوی حاصل از تولید محصولات ذکرشده استفاده میگردد.
الف) روش پنهانسازی Masking
در این روش با وارد نمودن مواد دیگر به هوای خروجی وجود بوی نا مطبوع را پوشانده و آنرا مخفی مینمایند.
ب) روش شستشو با آب
در این روش گازهای خروجی را درون برج شستشوی مرطوب (Wet Scrubbing) به طور تنگاتنگ با آب مخلوط مینمایند.
در این حال بوهای نامطبوع در آب حل و جذب میگردد و در نتیجه میزان آلودگی گاز خروجی کاهش مییابد در صورتی که در این روش تماس آب و هوا به خوبی تامین گردد این روش میتواند در بسیاری از موارد به سالمسازی هوای خروجی کمک کند. در این روش استفاده از مواد شیمیائی مانند هیپوکلریت سدیم و پرمنگنات پتاسیم و اوزن و دیگر عوامل اکسیدکننده معمول میباشد.
ج) روش سوزاندن
به نظر میرسد در حال حاضر مطلوبترین و موثرترین سیستم کنترل بو باشد. در این روش هوای خروجی را برای مدت ۱ تا ۲ دقیقه تا حدود ۷۰۰ تا ۸۰۰ درجه سانتیگراد گرم میکنند. در این حالت ترکیبات مولد بو اکسید میگردد.
در ارائه سیستم پیشنهادی ذیل از مزایای هر سه روش استفاده و از معایب آنها پرهیز شده است.
در این تحقیق روشی جهت کنترل صد درصد بوی نامطلوب ایجاد شده از تولید ارایه میشود. طراحی فرایند کنترل بو در روش ارایهشده بر اساس جداسازی ذرات جامد، میعان بخار آب خروجی و استفاده از مواد شیمیایی جهت تکمیل فرایند صورت پذیرفته است.
۱- سایکلون: عموماً برای جداسازی ذرات ریز جامد موجود در خروجی از دستگاههای دیوارهای و مبتنی بر راندن ذرات جامد به سوی یک دیواره –شامل انواع تهنشین کنندههای ثقلی– جدا سازیهای سنتری فوژی و الکتروفیلترها و همچنین وسایل جمعآوری، تقسیمکنندهها، مبتنی بر تقسیم ذرات جریان به قسمتهای کوچکتر، شامل انواع فیلترهای سطحی، فیلترهای عمقی و اسکرابرهای کنترل ذرات استفاده میشود. در این فرایند برای جداسازی ذرات جامد از سایکلون، جداساز سنتریفوژ استفاده میشود.
۲- مخزن جداکننده اولیه: بخارهای خروجی از تولید پس از هدایت به این مخزن به دو فاز بخار و مایع تبدیل میشوند. فاز بخار از بخش فوقانی مخزن به وسیله مکش ایجاد شده توسط پمپ خلاء موجود در خط به کندانسورها هدایت میشود و فاز مایع ایجاد شده از بخش تحتانی مخزن به سوی تصفیهخانه فاضلاب هدایت میگردد.
۳- کندانسورها: در این بخش با توجه به مقدار ظرفیت تعداد کندانسور طراحی میگردد که به دو صورت سری و موازی قرار میگیرد. این کندانسورها به صورت دسته لوله و پوسته طراحی شدهاند. که بخار خروجی به دسته لولهها هدایت میشود. سیال مبرد در پوسته جریان مییابد. فاز مایع خروجی از کندانسور بسمت جداکننده ثانویه میرود.
۴- برج خنک کن: سیال مبرد در کندانسورها آب میباشد. که برای کاهش دمای آن جهت بازگشت مجدد به مبدلها در یک سیکل بسته به مخزن بتنی با حجم حدود دویست متر مکعب که در مرکز ان برج خنک کن تعبیه شده است. هدایت میگردد.
۵- مخزن جداکننده ثانویه: این مخزن برای جداسازی مایع حاصل از کندانسورها از فاز بخار باقیمانده طراحی شده است. صفحات تعبیهشده در این مخزن و همچنین دیمیستر طراحی شده در بخش فوقانی آن از برادههای فلز جهت افزایش سطح تماس بخار استفاده شده است، در میعان موثرند. مایع حاصل از شیر تعبیهشده در بخش تحتانی مخزن به سمت تصفیهخانه فاضلاب هدایت میشود. بخارهای احتمالی خروجی به کویل میعان انتقال داده میشود.
۶- کویل میعان: این کویل بصورت یک لوله مارپیچ در مخزن حاوی آب سرد طراحی شده که بخار خروجی احتمالی را میعان میکند. خروجی از لوله کویل به قسمتهای بعدی هدایت میگردد.
۷- ستون سیلیکا ژل: این ستون بخاراتی را که به دلیل نوسانات دبی بخار در قسمتهای قبلی به مایع تبدیل نشدهاند را جذب میکند.
۸- ستون کربناکتیو: این ستون بخش تکمیلی ستون سیلیکا ژل میباشد. کربن موجود در این ستون توان جذب کامل مانده بخارات حاوی بو را دارا میباشد.
عمده بوی نامطلوب در فرایند تولید در مراحل تبخیر استیکواتر و پخت حاصل میگردد. خروجی از این بخش شامل بخار آب و ترکیبات آروماتیک و سولفید هیدروژن و تریمتیل آمین و… میباشد. این خروجی از لحاظ وزنی ۷۰ درصد ماده خام اولیه را بخود اختصاص میدهد.
روش پنهانسازی که به عنوان یکی از راههای کنترل بو میباشد با آنکه کارائی خوبی دارد ولی میتواند خود سبب ایجاد آلودگیهای جدیدی گردد. به علاوه همواره امکان جدا شدن مواد از یکدیگر وجود دارد. روش شستشو با آب اگر چه میتواند روش مناسبی جهت کنترل بو باشد. به طور مثال برج شستشوی کلر ۹۵ تا ۹۹ درصد راندمان دارد. ولی بالا بودن هزینه مواد شیمیائی و مشکل آلودگی ثانویه، آلودگی شیمیائی آب، استفاده از آن را محدود مینماید.
روش سوزاندن به عنوان مطلوبترین سیستم کنترل بو که تا ۱۰۰ درصد راندمان دارد به دلیل اتلاف حرارت و مصرف زیاد انرژی پرهزینه میباشد. در روشی مشابه برای کاهش مصرف سوخت از تماس مستقیم خروجی با شعله و هدایت به دودکشهای بلند استفاده میشود که راندمان حذف بو به دلیل زمان کم ماند در برابر حرارت و نوسان دبی خروجی در نتیجهعدم اکسید ترکیبات حاوی بو پائین میآید. استفاده از دودکش جهت ترقیق از آنجایی که آلودگی را کاهش نمیدهد بلکه تنها جابهجا میکند مردود میباشد.
در سیستم ارائه شده راندمان حذف بوی نامطلوب صد درصد میباشد که سهم درصدی راندمان در هر یک از بخشهای فرایند با در نظر گرفتن دمای محیط و فشار خروجی دیگ پخت در مخازن جداکننده گاز و مایع و سایکلونها ۱۵ درصد در مبدل حرارتی ۶۵ درصد و در کویل مبرد ۱۰ درصد و در ستونهای کربناکتیو و سیلیکا ژل ۵ درصد میباشد.
پساب ناشی از میعان بخار در مخازن جدا کننده اولیه و ثانویه و کویل میعان باید به تصفیهخانه هدایت شود. وجود تصفیه خانه فاضلاب با توجه به میزان و نوع پساب صنعتی حاصل از کشتار و فاضلاب بهداشتی ایجاد شده در کشتارگاههای دام و طیور و همچنین در کارخانجات تولید پودر ماهی ضروری میباشد.